فرم برنامه کنترل ویرایش سال 2024
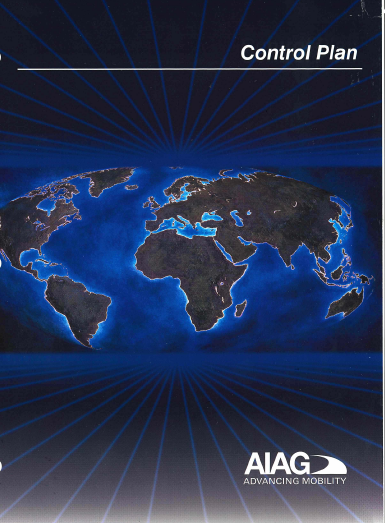
مشاوره پیاده سازی استانداردISO 17025:2017
- 1 (قسمت اول)Control Plan Reference Manual /AIAG APQP 2024
- 1.1 قسمت دوم نیز بزودی منتشر خواهد شد.
- 1.1.1 2.1 شروع به کار
- 1.1.2 2.2 زمان بندی و هماهنگی بین تیم های APQP و CP
- 1.1.3 2.3 ورودی ها( اعداد داخل پرانتز در قسمت زیر نشان دهنده قسمت مربوطه در کتابچه راهنمای APQP می باشد)
- 1.1.4 خروجی تحلیل ریسک محصول:
- 1.1.5 خروجی آنالیز(تحلیل) ریسک فرآیند:
- 1.1.6 شرح عملیات:
- 1.1.7 تاریخچه (ثبت سابقه) دانش کیفیت:
- 1.1.8 پارامترهای مهم:
- 1.1.9 نتایج بازنگری قابلیت سیستم:
- 1.1.10 طرح و فرکانس نمونه برداری:
- 1.1.11 خروجی های حاصل از صحه گذاری محصول و فرآیند:
- 1.1.12 استراتژی طرح واکنش:
- 1.1.13 شرکت عصر کیفیت -مشاور پیاده سازی IATF 16949
- 1.2 ادامه در قسمت دوم …بزودی
- 1.1 قسمت دوم نیز بزودی منتشر خواهد شد.
(قسمت اول)Control Plan Reference Manual /AIAG APQP 2024
قسمت دوم نیز بزودی منتشر خواهد شد.
همانطور که مستحضرید ویرایش سوم راهنمای تکوین محصول توسط AIAG در سال 2024 منتشر شد.به همراه آن پیوست برنامه کنترل نیز منتشر گردید.قطعا تصدیق می فرمایید که برنامه کنترل نقش اساسی در تکوین محصول و مدارک SQA دارد و فرمت آن بین سایپا و ساپکو و سازه گستر و کرمان موتور و … نیز یکسان است.
هدف یک طرح کنترل تسهیل ارتباط با همه افراد درگیر است تا اطمینان حاصل شود که همه کنترلهای مورد نیاز به موقع و به طور کامل در هر بار تکمیل میشوند.
اثربخشی طرح کنترل بستگی به تعهد رهبری شرکت، به تلاش لازم برای دستیابی به رضایت مشتری دارد.
هر طرح کنترلی منحصر به فرد است. زمان و ترتیب واقعی اجرا به نیازها و انتظارات مشتری و/یا سایر موارد عملی بستگی دارد.
هر چه زودتر یک تمرین کاری، ابزار، و/یا تکنیک تحلیلی را بتوان در چرخه برنامه ریزی کیفیت محصول پیاده سازی کرد، بهتر است.
این فصل نحوه گرفتن خروجی از مراحل قبلی در فرآیند برنامه ریزی کیفیت محصول (طبق کتابچه راهنمای AIAG APQP) برای توسعه سند طرح کنترل را شرح می دهد.
ورودی ها و خروجی های قابل اعمال در فرآیند توسعه طرح کنترل ممکن است با توجه به فرآیند توسعه محصول و نیازها و انتظارات مشتری متفاوت باشد. فهرست ورودیها و خروجیهای ارائهشده بهمنظور فراگیر بودن(کلی) نیست، بلکه برای ارائه مثالهایی از اطلاعات موردی به کار رفته شده است.
هدف از فرم طرح کنترل نمایش داده شده در این فصل ارائه مثالی از نحوه مستندسازی این اطلاعات است. اگر حداقل حاوی همان اطلاعات در این فرم باشد، ممکن است از بتوان از یک قالب جایگزین استفاده کرد.
2.1 شروع به کار
فرآیند برنامه کنترل و تیم، بخشی از فعالیت برنامه ریزی پیشاپیش کیفیت محصول سازمان است که در کتابچه راهنمای AIAG APQP:2024 به آن اشاره شده است.
بر این اساس، فرآیند طرح کنترل با مراحل ذکر شده در کتابچه راهنمای APQP شروع می شود (برای جزئیات بیشتر، به کتابچه راهنمای AIAG APQP مراجعه کنید).
- سازماندهی تیم: اولین گام سازمان تعیین مالک فرآیند برای طرح کنترل است. یک تیم چند تخصصی (رهبری، مهندسی، تولید، کیفیت، تامین کنندگان و غیره) باید تعیین شود. ممکن است لازم باشد تیم ها یا نمایندگان مختلفی برای مراحل مختلف برنامه کنترل داشته باشیم (به عنوان مثال، تیم CP پیش از تولید ممکن است با تیم CP تولید متفاوت باشد).
- اسکوپ (دامنه کاری) را تعریف کنید: در ابتدایی ترین مرحله برنامه، شناسایی نیازها، انتظارات و الزامات مشتری برای تیم توسعه طرح کنترل سازمان مهم است. تیم همچنین باید امکان سنجی آزمایش ها و کنترل های پیشنهادی تجویز شده در طراحی، الزامات عملکرد و فرآیند ساخت را ارزیابی کند. در برخی موارد، ممکن است تیم، نیاز به کمک مورد نیاز از مشتری را تعیین کند.
- تیم به تیم (خطوط ارتباط): تیم برنامه کنترل باید خطوط ارتباطی با تیم های قابل اجرای(بالقوهیا محتمل) مشتری، سازمان و تامین کننده را ایجاد کند.
- آموزش: موفقیت در توسعه طرح کنترل به یک برنامه آموزشی مؤثر بستگی دارد که تمام الزامات و مهارت های توسعه را برای برآورده ساختن نیازها و انتظارات مشتری به اشتراک می گذارد.
- مشارکت مشتری و سازمان: مشتری اصلی(اولیه) ممکن است فرآیند توسعه طرح کنترل را آغاز کند، اما سازمان موظف به مدیریت توسعه طرح کنترل است و باید همان عملکرد را از تامین کنندگان خود بخواهد.
2.2 زمان بندی و هماهنگی بین تیم های APQP و CP
تیم فرآیند طرح کنترل باید فعالیت های خود را با تیم فرآیند APQP هماهنگ کند، در درجه اول با اطمینان از همسویی نقاط عطف و قابل تحویل با برنامه زمان بندی کیفیت محصول همانطور که در کتابچه راهنمای AIAG APQP تعریف شده است.
موارد کلیدی که باید در نظر گرفته شوند شامل، اما محدود به آن نیستند (برای جزئیات هر کدام به راهنمای تکوین محصول AIAG مراجعه کنید)
- مهندسی همزمان: در جایی که در آن نتایج برای اجرا به ناحیه بعدی منتقل می شود، ترتیب متوالی فازها جابجا میگردد.تیم توسعه طرح کنترل سازمان، هماهنگی با گروه های مرتبط را برای به دست آوردن ورودی ها و ارائه خروجی ها بر اساس طرح کلی APQP تضمین می کند.
- حل نگرانی: نگرانی های مربوط به توسعه طرح کنترل باید در یک ماتریس با مسئولیت و زمان تعیین شده ثبت شود.
- برنامه زمانبندی کیفیت محصول: مالک فرآیند برای توسعه طرح کنترل باید از برنامه زمانبندی کیفیت محصول که توسط مالک فرآیند APQP تهیه شده است، از جمله تغییرات در طرح، پشتیبانی کرده و از آن مطلع شود. نظارت بر برنامه گزارشدهی مؤثر وضعیت با تمرکز بر شناسایی مواردی که نیاز به توجه ویژه دارند.
- برنامه های مربوط به نمودار زمان بندی: تیم توسعه برنامه کنترل سازمان مسئول اطمینان از مطابقت با زمان بندی قابل تحویل یا جلوتر بودن از نمودار زمان بندی کیفیت محصول است که توسط مالک فرآیند APQP ایجاد و نگهداری می شود.
2.3 ورودی ها( اعداد داخل پرانتز در قسمت زیر نشان دهنده قسمت مربوطه در کتابچه راهنمای APQP می باشد)
- تیم چند رشته ای یا چند تخصصی
- تجربه تیمی (1.1.3).
- پشتیبانی رهبری
- (14، 2.13، 3.10، 4.8)
- لیست تمام تامین کنندگان.
خروجی تحلیل ریسک محصول:
- DFMEA (2.1).
- فهرست عملکرد/ویژگیهای عملکردی محصول از طراحی (DFMEA)، و تستهای مربوطه و الزامات ابعادی.
- نقشه های مهندسی (2.6)، از جمله GD&T.
- ویژگی های نقشه های مهندسی و مشخصات مواد (2.8).
- فهرست دستگاهها/مکانیسمهای خطاناپذیری برای هر حالت عملیات/عیب و ویژگیهای محصول/فرآیند
- طراحی برای تولید، طراحی برای مونتاژ، وطراحی برای خدمات (2.2).
- مشخصات مواد (2.8)، از جمله الزامات جابجایی و ذخیره سازی، و مواردی که نیاز به بازرسی دارند.
خروجی آنالیز(تحلیل) ریسک فرآیند:
- PFMEA (3.5).
- کنترل های PFMEA، از جمله لیست و توالی فرآیندهای مربوطه.
- تحلیل و اقدامات PFMEA معکوس.
- فهرستی از دستگاه ها/مکانیسم های ضد خطا در هر حالت عملیات/عیب و ویژگی های محصول/فرآیند که بررسی می کند.
- فهرست روش های تشخیص برای هر عملیات/نوع نقص.
- شناسایی عملیات تعمیر/دوباره کاری/استفاده مجدد.
شرح عملیات:
- نمودار جریان فرآیند Process Flow Chart (1.10, 3.3).
- چیدمان پلان طبقه Floor Plan Layout (3.4).
- طرح بندی ابزار. Tool Layout
- ملاحظات محیط ایستگاه کاری (به عنوان مثال، نور) و ارگونومی.
- تجهیزات جدید، ابزار و امکانات مورد نیاز (2.10).
تاریخچه (ثبت سابقه) دانش کیفیت:
- درس های آموخته شده از قسمت های مشابه.
- نظارت بر طرح کنترل برای فرآیندهای مشابه/کارخانه های مشابه
- ارزیابی های فرآیند.
- سوابق وارانتی واطلاعات کیفی (1.1.2).
پارامترهای مهم:
- شناسایی پارامترهای مهم محصول و فرآیند (1.11، 2.11)، از جمله الزامات ایمنی و قانونی.
نتایج بازنگری قابلیت سیستم:
- بازنگری سیستم کیفیت محصول/فرآیند (3.2).
- گیج ها و تجهیز(وسیله) اندازه گیری توانمند.
- لیست قابلیت های گیج.
- فرآیند مدیریت تغییر و سوابق بازنگری موجود باشد.
- ابزاری برای پایش عملیات پایان خط. monitor end of line operations
- پایش قابلیت های فرآیند.
طرح و فرکانس نمونه برداری:
- پارامترهای مهندسی (2.7)، به خصوص اگر “ایستگاه تست در حین فرآیند” باشد شامل اندازه نمونه، فراوانی و معیارهای پذیرش .
- ملاحظات صحه گذاریpart First-off و Last-off part
- پروتکل هایی برای تغییر روش تولید و راه اندازی مجدد فعالیت ها (تغییر ابزار، تعمیر و نگهداری، خاموش کردن یا اصطلاحا shutdown و غیره).
خروجی های حاصل از صحه گذاری محصول و فرآیند:
- یک دوره تولید مداوم (4.1).
- تجزیه و تحلیل سیستم اندازه گیری (4.2).
- مطالعه قابلیت فرآیند مقدماتی (4.3).
- تست صحه گذاری تولید (4.5).
- نتایج تولید “یک روز خط pre-Launch” و/یا “راه اندازی ایمن safe-Launch”.
Safe Launch ابزار مهمی برای دستیابی به این هدف است که تست و صحه گذاری را برای شناسایی و رسیدگی به مسائل بالقوه ایمنی و کیفیت قبل از عرضه محصولات به بازار و سپس اعمال اقدامات اصلاحی در فرآیند تولید ارائه میکند.
استراتژی طرح واکنش:
- بر أساس نوع عیب
گروه بندی بر أساس نوع عیوب شناخته شده (به عنوان مثال، کلیه عیوب شناخته شده در بازرسی 100٪ که اپراتور برای تعیین تکلیف محصول معیوب آموزش دیده است).
- بر أساس تعداد عیب
گروه بندی بر أساس فلان( X ) تعداد عیوب در یک ردیف (اپراتوری که عیب را تشخیص داده است ، چه اقدامی میتواند انجام دهد، قبل از اعلام به سرپرست)
توضیحات مرتبط با فرم جدید برنامه کنترل CONTRP PLAN FORM 2024
شماره یک تا هفت که واضح است و از شماره 8 به بعد شروع می کنیم:
8. تاریخ تایید تامین کننده/کارخانه
تأییدیه کارخانه)بخش) عهده دارتولید در سازمان را دریافت کنید (در صورت نیاز به الزامات خاص مشتری مراجعه کنید).
- تاریخ (اصلی)
تاریخ تدوین برنامه کنترل اصلی(اولیه) را وارد کنید.
- تاریخ (Rev.)
تاریخ آخرین به روز رسانی های طرح کنترل را وارد کنید.
11. تایید مهندسی مشتری / تاریخ
تأییدیه مهندسی مشتری را دریافت کنید (در صورت نیاز به الزامات مقتضی خاص مشتری مراجعه کنید).
- تایید کیفیت مشتری/تاریخ
تاییدیه نماینده کیفیت تامین کننده مشتری را دریافت کنید (در صورت لزوم به الزامات مقتضی خاص مشتری مراجعه کنید).
13. سایرتاییدیه ها /تاریخ
هر گونه موافقت دیگری را پس از تایید دریافت کنید (در صورت نیاز).
- شماره قطعه/فرآیند
شماره این قسمت معمولاً از نمودار جریان فرآیند ارجاع داده می شود. اگر چندین شماره قطعه وجود دارد (مونتاژ)، شماره قطعات و فرآیندهای آنها را فهرست کنید.
- نام فرآیند/شرح عملیات
تمام مراحل ساخت یک سیستم، زیرسیستم یا اجزا آن در یک نمودار جریان فرآیند توضیح داده شده است. نام فرآیند/عملیات را از نمودار جریان فرآیند شناسایی کنید به نحوی که فعالیتی را که به آن پرداخته می شود، به بهترین وجه توصیف می کند.
- ماشین، دستگاه، جیگ و ابزار برای ساخت
برای هر عملیاتی که شرح داده می شود، نوع تجهیزات فرآیند را مشخص کنید، مانند مدل برند ماشین، نوع فیکسچر یا سایر توضیحات مرتبط با ابزارآلات تولیدی.
شرکت عصر کیفیت -مشاور پیاده سازی IATF 16949
تعاریف و توضیحات مرتبط با قسمتهای 17 تا 19
یک ویژگی متمایز، بعد یا ویژگی یک فرآیند یا خروجی (محصول) آن که می توان داده های کمی یا کیفی را بر اساس آن جمع آوری کرد.
نمودارهای جریان فرآیند بایستی برای مکان یابی ویژگی های مهم محصول و فرآیند که در طرح کنترل به آن پرداخته می شود استفاده شود. علاوه بر این، از DFMEA، در صورتی که موجود باشد ، برای شناسایی ویژگی های مهمی که ممکن است به عنوان ویژه طبقه بندی شوند، استفاده کنید.
تمام اسناد قابل اجرا مانند، اما نه محدود به، نمودارهای جریان فرآیند، نقشه های ساخت شماره گذاری شده، FMEA، مشخصات مهندسی و مواد، و نقشهها یا سایر استانداردهای بصری، بایستی برای تهیه فهرستی از ویژگیها استفاده شوند. سازمان بایستی تعیین کند که کدام ویژگی ها بر برآوردن الزامات عملکردی، دوام و ظاهر تأثیر می گذارد و آنها را در برنامه کنترل درج کند.
فرم مشخصات مهم (محصول یا فرآیند)، بعنوان پایه و اساس تکمیل این ستون که شامل تمام مشخصات مهم فرآیند و محصول است توسط تیم چندتخصصی بکار گرفته میشود. است که توسط تیم متقابل توافق شده است. در فرم برنامه کنترل، یک عدد ترتیبی (شماره) به هر یک از ویژگی های فهرست شده اختصاص داده می شود تا اطمینان حاصل شود که هیچ یک از آنها توسط سازمان در هنگام تکمیل برنامه کنترل نادیده گرفته نمی شود.(مانند 1-1 و 1-2 و …2-1 و 2-2 و …)
این اطلاعات در طرح کنترل برای هر مشخصه، تحت عنوان(در ستون ) “فرآیند” و/یا “محصول” مربوطه وارد می شود.
- مشخصات – شماره
در صورت نیاز، یک شماره cross reference number) ) به تمام اسناد قابل اجرا مانند، اما نه محدود به، نمودارهای جریان فرآیند، نقشه های ساخت شماره گذاری شده ، FMEA و نقشهها یا سایر استانداردهای بصری اختصاص دهید. فرم های نمونه اختیاری و توضیح این فرمها در ضمیمه B، B.3 قرار دارد. فرم مشخصات مهم.
cross reference number : ابتدا باید در سایت
عضو شوید.کراس رفرنس از ناشران می خواهد تا رفرنس های خود را در مجلات همراه با کد DOI ذکر کنند که برای آن ۶ روش پیشنهاد می کند که از ضروریات عضویت می باشد این ۶ روش با ذکر مثال برای هر کدام را می توانید از اینجا ببینید. برای مثال آوردن آدرس اینترنتی یا URLمربوط به DOI، قرار دادن این آدرس به صورت هایپرلینک در لوگوی کراس رفرنس، قرار دادن لگوی حاوی لینک قبل از آدرس کد، قرار دادن متن کرای رفرنس حاوی لینک، گذاشتن اسم هایی مثلArticle و یا ful text که حاوی لینک هستند و یا اتقاده از میانبر برای کد DOI که Short DOIنامیده می شود.
همچنین لازم به ذکر است که افزار word این گزینه را در قسمت Insert-Cross-reference دارد.
- مشخصات – محصول
مشخصات محصول، ویژگی ها یا مشخصات یک قطعه، جزء یا مجموعه است که در نقشه ها یا سایر اطلاعات مهندسی اصلی توضیح داده شده است. تیم اصلی بایستی مشخصه های مهم محصول را که مجموعه ای از ویژگی های مهم محصول بدست آمده از همه منابع هستند را شناسایی کند. تمام مشخصات مهم (ویژه) باید در طرح کنترل درج شود. علاوه بر این، سازمان ممکن است مشخصات محصول دیگری را که کنترل های فرآیند به طور معمول(روتین) در طول عملیات نرمال ردیابی می شوند فهرست کند.
- مشخصات – فرآیند
مشخصات فرآیند، متغیرهای فرآیندی (متغیرهای ورودی) هستند که رابطه علت و معلولی با ویژگی محصول شناسایی شده دارند. یک مشخصه فرآیند فقط در زمان وقوع قابل اندازه گیری است. تیم اصلی باید مشخصات فرآیند را با هدف کنترل پراکندگی شناسایی کند.به طوری که پراکندگی محصول حداقل گردد.
ممکن است یک یا چند مشخصه فرآیند برای هر مشخصه محصول ذکر شده باشد. در برخی فرآیندها یک مشخصه فرآیند ممکن است بر چندین مشخصه محصول تأثیر بگذارد.(از ماتریس سوم QFD میتوان کمک گرفت)
- طبقه بندی مشخصه ویژه
از طبقه بندی مناسب مطابق خواسته مشتری استفاده کنید (به الزامات خاص مشتری مناسب مراجعه کنید)، نوع مشخصه مهم را تعیین کنید یا این فیلد را می توان برای سایر مشخصه های تعیین نشده خالی گذاشت. مشتریان ممکن است از نمادهای منحصر به فرد برای شناسایی ویژگی های مهم استفاده کنند، مانند مواردی که بر ایمنی مشتری، انطباق با مقررات، شکل، تناسب، عملکرد و غیره تأثیر می گذارد.
دیدگاهتان را بنویسید