دستوالعمل کار استاندارد جوشکاری و AIAG CQI 15
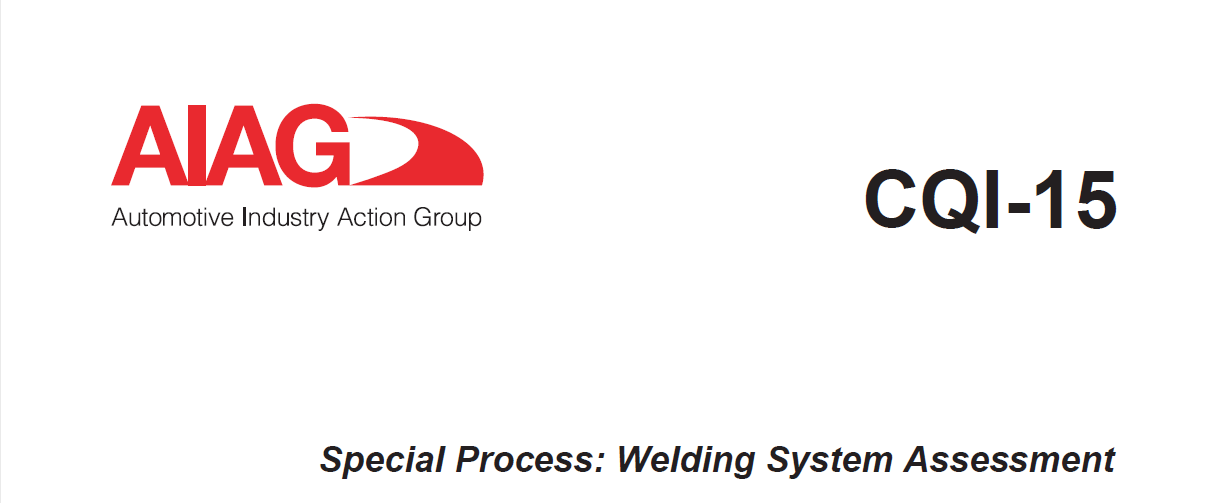
مشاوره پیاده سازی استانداردISO 17025:2017
- 1 **دستورالعمل کار استاندارد جوشکاری نقطهای فلزات**
- 2 **آمادهسازی قطعات در خودروسازی و استاندارد IATF 16949:2016**
- 3 **تنظیم دستگاه جوشکاری و بررسی موردی بر اساس استاندارد CQI-15 AIAG و IATF 16949:2016**
- 4 دانلود IATF 16949 AIAG CQI 15
- 5 پارامترهای موثر بر میزان و تنظیم جریان الکتریکی در جوش نقطهای
- 6 زمان جوشکاری
- 7 فشار الکترودها :
- 8 دانلود کتاب جوشکاری
**دستورالعمل کار استاندارد جوشکاری نقطهای فلزات**
**1. مقدمه:**
جوشکاری نقطهای یکی از روشهای متداول جوشکاری است که بهطور وسیع در صنایع خودروسازی، هوافضا، و تولید محصولات فلزی مورد استفاده قرار میگیرد. در این روش، از دو الکترود برای گرم کردن و ذوب کردن سطح تماس دو فلز استفاده میشود تا یک نقطه جوش تشکیل شود.
**2. تجهیزات و ابزار مورد نیاز:**
– دستگاه جوشکاری نقطهای (Spot Welding Machine)
– الکترودهای جوشکاری (مس یا آلیاژ مس)
– قطعات فلزی مورد نیاز
– گیرهها و نگهدارندههای قطعه
– دستکش و عینک ایمنی
**3. آمادهسازی قطعات:**
– قطعات فلزی باید تمیز، خشک و عاری از زنگزدگی، روغن یا هرگونه آلودگی باشند.
– اطمینان حاصل کنید که ضخامت قطعات فلزی مناسب برای جوشکاری نقطهای است.
– قطعات را با گیرهها یا نگهدارندهها بهصورت دقیق در موقعیت مورد نظر قرار دهید.
**4. تنظیم دستگاه جوشکاری:**
– جریان الکتریکی دستگاه را براساس ضخامت و نوع فلز تنظیم کنید. (معمولاً بین 1000 تا 10,000 آمپر)
– زمان اعمال جریان و فشار الکترودها را متناسب با نوع فلز و ضخامت آن تنظیم کنید.
**5. اجرای جوشکاری:**
– قطعات را بین الکترودهای دستگاه قرار دهید.
– فشار مناسب الکترودها را اعمال کنید تا تماس کامل برقرار شود.
– جریان الکتریکی را برای مدت زمان معین اعمال کنید تا نقطه جوش شکل گیرد.
– پس از اتمام جوشکاری، الکترودها را بردارید و اجازه دهید قطعات خنک شوند.
**6. بازرسی و کنترل کیفیت:**
– پس از جوشکاری، نقطه جوشها را از نظر شکل ظاهری و کیفیت بررسی کنید.
– از آزمونهای غیرمخرب مانند تست برشی یا کششی استفاده کنید تا اطمینان حاصل شود که جوشها از استحکام کافی برخوردار هستند.
**7. ایمنی:**
– همواره از دستکش، عینک و لباسهای محافظ استفاده کنید.
– از تماس مستقیم با قطعات داغ و الکترودها خودداری کنید.
– محیط کار باید دارای تهویه مناسب باشد تا از استنشاق دودهای مضر جلوگیری شود.
**8. نگهداری و تعمیرات:**
– الکترودها را بهطور منظم تمیز و تیز کنید.
– دستگاه جوشکاری را طبق دستورالعمل سازنده سرویس و نگهداری کنید.
**9. مستندسازی:**
– تمامی پارامترهای جوشکاری مانند جریان، زمان و فشار را ثبت کنید.
– نتایج تستهای کیفیت را مستند کنید تا در صورت نیاز به بهبود فرآیند، مرجع دقیقی داشته باشید.
**10. خاتمه:**
پس از اتمام کار، دستگاه را خاموش کنید و محل کار را تمیز کنید. مطمئن شوید که قطعات جوشکاری شده بهطور کامل خنک شدهاند و آماده استفاده یا انتقال به مراحل بعدی تولید هستند.
دانلود آيين نامه ايمني جوشكاري و برشكاري گرم
آیین-نامه-ایمنی-جوشکاری-و-برشکاری-نرم
**آمادهسازی قطعات در خودروسازی و استاندارد IATF 16949:2016**
**1. مقدمه:**
آمادهسازی قطعات در فرآیند تولید خودرو، بهویژه در جوشکاری نقطهای، از اهمیت بسیار بالایی برخوردار است. استاندارد IATF 16949:2016 که ویژه صنعت خودروسازی تدوین شده است، تأکید زیادی بر کیفیت و رعایت الزامات فرآیندهای تولیدی دارد. این استاندارد، همسویی با ISO 9001 را حفظ کرده و موارد خاص صنعت خودرو را پوشش میدهد.
**2. اهمیت آمادهسازی قطعات:**
در فرآیندهای تولیدی خودرو، آمادهسازی مناسب قطعات، کلید دستیابی به کیفیت مطلوب در جوشکاری و سایر مراحل تولید است. هرگونه نقص در این مرحله میتواند منجر به تولید قطعات معیوب و افزایش ضایعات شود.
**3. الزامات IATF 16949:2016 برای آمادهسازی قطعات:**
1. **تمیزی و آمادهسازی سطوح:**
– قطعات فلزی باید بهطور کامل از هرگونه آلودگی مانند زنگزدگی، چربی، روغن و گرد و غبار پاک شوند.
– از روشهای شیمیایی یا مکانیکی مانند شستشو، ساب زدن و استفاده از حلالها برای پاکسازی سطوح استفاده میشود.
– کنترلهای لازم برای اطمینان از تمیزی قطعات پیش از ورود به مراحل بعدی تولید باید برقرار باشد.
2. **بازرسیهای دورهای:**
– مطابق با استاندارد IATF 16949، بازرسیهای دورهای برای بررسی تمیزی و کیفیت سطوح قطعات قبل از ورود به مراحل جوشکاری ضروری است.
– مستندسازی و ثبت نتایج بازرسی برای ردیابی و تحلیل کیفیت ضروری است.
3. **آموزش و صلاحیت پرسنل:**
– پرسنل مسئول آمادهسازی قطعات باید دارای آموزشهای لازم در زمینه روشهای تمیزکاری و الزامات کیفی باشند.
– سیستمهای مدیریت آموزش باید مستند شوند تا اطمینان حاصل شود که کارکنان بهطور مداوم بهروزرسانی شدهاند.
4. **کنترل محیطی:**
– محیط کار باید بهگونهای طراحی و نگهداری شود که مانع از آلودگی مجدد قطعات پس از تمیزکاری شود.
– از تجهیزات کنترل محیطی مانند فیلترهای هوا و سیستمهای تهویه استفاده شود تا کیفیت محیط کار بهینه بماند.
**تنظیم دستگاه جوشکاری و بررسی موردی بر اساس استاندارد CQI-15 AIAG و IATF 16949:2016**
**1. مقدمه:**
تنظیم دقیق دستگاه جوشکاری در فرآیند تولید، بهویژه در صنعت خودروسازی، یکی از عوامل کلیدی برای دستیابی به کیفیت مطلوب جوش و کاهش نقصها است. استاندارد IATF 16949:2016 و معیارهای ویژه خودروسازی مانند CQI-15 که توسط AIAG تدوین شده، الزامات خاصی را برای کنترل فرآیند جوشکاری ارائه میدهند.
**2. الزامات استاندارد CQI-15 و IATF 16949 برای تنظیم دستگاه جوشکاری:**
**2.1. معیارهای تنظیم دستگاه:**
– **جریان الکتریکی:** تنظیم جریان الکتریکی (آمپر) باید مطابق با نوع فلز و ضخامت آن انجام شود. جریان باید بهگونهای تنظیم شود که نقطه جوش مطلوب بدون سوختگی یا ضعف ایجاد شود.
– **زمان جوشکاری:** مدت زمان اعمال جریان الکتریکی باید متناسب با ویژگیهای قطعات و نوع جوشکاری باشد.
– **فشار الکترودها:** فشار اعمال شده توسط الکترودها باید به اندازهای باشد که تماس کامل بین قطعات برقرار شده و کیفیت جوش تضمین شود.
– **شکل و تمیزی الکترودها:** الکترودها باید بهطور منظم تمیز و در صورت نیاز تیز شوند تا کیفیت جوش حفظ شود.
**2.2. کنترل و پایش فرآیند:**
– **پایش مستمر:** فرآیند جوشکاری باید بهطور مداوم پایش شود تا اطمینان حاصل شود که پارامترهای تنظیم شده در طول زمان ثابت باقی میمانند.
– **استفاده از ابزارهای کنترلی:** از ابزارهای اندازهگیری و پایش جریان، فشار و زمان استفاده شود تا تنظیمات دستگاه بهدرستی انجام شده و نظارت بر آنها ادامه یابد.
– **ثبت سوابق:** تمامی تنظیمات دستگاه و نتایج پایش باید ثبت و مستند شوند تا در صورت نیاز به تحلیل یا بازبینی، اطلاعات کافی در دسترس باشد.
**2.3. الزامات آموزشی:**
– **آموزش پرسنل:** پرسنل مسئول تنظیم و پایش دستگاههای جوشکاری باید آموزشهای لازم را دیده و صلاحیت کافی برای انجام این کار داشته باشند.
– **بازبینی و بهروزرسانی آموزشها:** دورههای آموزشی باید بهطور منظم بازبینی و بهروزرسانی شوند تا با تغییرات تکنولوژیکی و استانداردهای جدید هماهنگی داشته باشند.
**3. مثال موردی بر اساس CQI-15 و IATF 16949:**
**مثال: تنظیم دستگاه جوشکاری نقطهای برای بدنه خودرو (بدنه خودرو از جنس فولاد کمکربن)**
**3.1. تعریف پارامترها:**
– **جریان الکتریکی:** برای فولاد کمکربن با ضخامت 1.5 میلیمتر، جریان الکتریکی باید بین 8000 تا 9000 آمپر تنظیم شود.
– **زمان جوشکاری:** زمان جوشکاری باید بین 0.2 تا 0.5 ثانیه تنظیم شود.
– **فشار الکترودها:** فشار باید بهگونهای تنظیم شود که دو قطعه بهطور کامل تماس داشته باشند، معمولاً بین 300 تا 500 نیوتن.
**3.2. پایش و کنترل:**
– **اندازهگیریهای اولیه:** با استفاده از دستگاههای پایش، جریان، فشار و زمان اندازهگیری شده و با پارامترهای تعیین شده مقایسه میشود.
– **تستهای جوش:** پس از انجام تنظیمات، چندین تست جوش انجام میشود و کیفیت جوشها از نظر ظاهری و مکانیکی بررسی میشود.
– **کنترل کیفیت:** جوشهای ایجاد شده تحت آزمونهای غیرمخرب مانند تست برشی یا کششی قرار میگیرند تا استحکام و یکپارچگی آنها تایید شود.
**3.3. مستندسازی:**
– **ثبت تنظیمات:** تمامی تنظیمات انجام شده برای دستگاه جوشکاری ثبت و مستند میشوند.
– **گزارش تستهای کیفیت:** نتایج تستهای انجام شده ثبت و به عنوان مرجع در فرآیند تولید نگهداری میشوند.
**4. نتیجهگیری:**
با توجه به اهمیت تنظیم دقیق دستگاههای جوشکاری و پایش مداوم آنها، استانداردهای CQI-15 AIAG و IATF 16949:2016 چارچوبهای محکمی برای تضمین کیفیت فرآیندهای جوشکاری در صنعت خودروسازی ارائه میدهند. اجرای دقیق این الزامات به کاهش نقصها، بهبود کیفیت و رضایت مشتریان کمک میکند.
**دستورالعمل جوشکاری قطعات فلزی خودرو: مثال درب خودرو**
**1. مقدمه:**
جوشکاری قطعات فلزی در صنعت خودروسازی از اهمیت بسیار بالایی برخوردار است، زیرا کیفیت جوش تأثیر مستقیم بر ایمنی و استحکام خودرو دارد. این دستورالعمل برای جوشکاری درب خودرو که از جنس فولاد کمکربن است، تدوین شده است.
**2. تجهیزات و ابزار مورد نیاز:**
– دستگاه جوشکاری نقطهای (Spot Welding Machine)
– الکترودهای جوشکاری (مس یا آلیاژ مس)
– گیرهها و نگهدارندههای قطعه
– ابزارهای اندازهگیری جریان، فشار، و زمان
– دستکش، عینک ایمنی و لباس محافظ
**3. آمادهسازی قطعات:**
– قطعات درب خودرو باید قبل از جوشکاری از هرگونه آلودگی مانند روغن، گرد و غبار و زنگزدگی پاک شوند.
– از روشهای شیمیایی (شستشو با حلال) یا مکانیکی (ساب زدن) برای تمیز کردن سطوح استفاده کنید.
– قطعات را با دقت و استفاده از گیرهها در موقعیت صحیح قرار دهید تا از تطابق دقیق آنها اطمینان حاصل شود.
**4. تنظیم دستگاه جوشکاری:**
**4.1. پارامترهای جوشکاری:**
– **جریان الکتریکی:** برای فولاد کمکربن با ضخامت 1.2 تا 1.5 میلیمتر، جریان الکتریکی دستگاه باید بین 8000 تا 9000 آمپر تنظیم شود.
– **زمان جوشکاری:** زمان جوشکاری باید بین 0.3 تا 0.5 ثانیه باشد.
– **فشار الکترودها:** فشار الکترودها باید بین 350 تا 450 نیوتن تنظیم شود تا از تماس کامل قطعات اطمینان حاصل شود.
**4.2. بررسی و کنترل اولیه:**
– **اندازهگیری پارامترها:** با استفاده از ابزارهای پایش، جریان، زمان و فشار اندازهگیری شده و با مقادیر تنظیم شده مقایسه شود.
– **بازرسی بصری:** مطمئن شوید که الکترودها تمیز و بدون آسیب هستند. در صورت نیاز، الکترودها را تعویض یا تمیز کنید.
**5. اجرای جوشکاری:**
– قطعات درب خودرو را در محل جوشکاری قرار دهید و با گیرهها محکم کنید.
– الکترودهای دستگاه را بر روی نقاط مورد نظر قرار دهید و فشار لازم را اعمال کنید.
– جریان الکتریکی را به مدت زمان معین اعمال کنید تا نقطه جوش ایجاد شود.
– پس از جوشکاری، اجازه دهید قطعات کمی خنک شوند و سپس آنها را از دستگاه خارج کنید.
**6. بازرسی و کنترل کیفیت:**
– پس از جوشکاری، نقطه جوشها را از نظر کیفیت ظاهری بررسی کنید. جوشها باید یکنواخت و بدون سوختگی یا نقص باشند.
– از آزمونهای غیرمخرب مانند تست برشی یا کششی استفاده کنید تا استحکام جوشها را بررسی کنید.
– در صورت وجود نقص، فرآیند جوشکاری باید متوقف و تنظیمات دستگاه بررسی شود.
**7. مستندسازی:**
– تمامی پارامترهای جوشکاری مانند جریان، زمان، و فشار را ثبت کنید.
– نتایج بازرسیها و تستهای کیفیت را مستند کنید تا در صورت نیاز به تحلیل یا بازبینی، اطلاعات کافی در دسترس باشد.
**8. ایمنی:**
– همواره از تجهیزات ایمنی مانند دستکش، عینک و لباسهای محافظ استفاده کنید.
– از تماس مستقیم با قطعات داغ و الکترودها خودداری کنید.
– محیط کار باید دارای تهویه مناسب باشد تا از استنشاق دودهای جوشکاری جلوگیری شود.
**9. خاتمه:**
پس از اتمام جوشکاری، دستگاه را خاموش کرده و محل کار را تمیز کنید. مطمئن شوید که قطعات جوشکاری شده بهطور کامل خنک شدهاند و آماده برای انتقال به مراحل بعدی تولید هستند.
**10. نتیجهگیری:**
این دستورالعمل با توجه به استانداردهای کیفی و ایمنی تدوین شده است تا کیفیت و ایمنی در فرآیند جوشکاری درب خودرو تضمین شود. رعایت دقیق این دستورالعمل به بهبود کیفیت محصول نهایی و افزایش رضایت مشتریان کمک میکند.
دانلود چک لیست نقطه جوش مقاومتی گروه سایپا پیوست 16 SSQR 2
**AIAG CQI-15: خلاصهای از استاندارد**
**1. مقدمه:**
AIAG CQI-15 یک راهنمای تخصصی برای ارزیابی سیستمهای جوشکاری مقاومتی (از جمله جوشکاری نقطهای) در صنعت خودروسازی است. این استاندارد توسط AIAG (Automotive Industry Action Group) تدوین شده و هدف آن کمک به تأمینکنندگان خودرو برای اطمینان از کیفیت و کارایی فرآیندهای جوشکاری است.
**2. هدف:**
هدف CQI-15 بهبود مستمر فرآیندهای جوشکاری مقاومتی، کاهش نقصها و تضمین کیفیت قطعات جوشکاری شده است. این استاندارد به تأمینکنندگان کمک میکند تا سیستمهای جوشکاری خود را ارزیابی، کنترل و بهینهسازی کنند.
**3. الزامات اصلی:**
– **ارزیابی فرآیند:** فرآیند جوشکاری باید بهطور مداوم ارزیابی شود تا از کارایی و کیفیت آن اطمینان حاصل شود.
– **کنترل پارامترها:** پارامترهای مهم جوشکاری مانند جریان الکتریکی، فشار الکترودها، و زمان جوشکاری باید کنترل و ثبت شوند.
– **بازرسی و تست:** تمامی جوشهای تولیدی باید تحت بازرسی و آزمونهای غیرمخرب قرار گیرند تا کیفیت آنها تایید شود.
– **مستندسازی:** تمامی مراحل و نتایج ارزیابی و تست باید مستند شوند تا قابلیت ردیابی و تحلیل وجود داشته باشد.
– **آموزش و صلاحیت پرسنل:** کارکنان مرتبط با فرآیند جوشکاری باید آموزش دیده و صلاحیت لازم را برای انجام وظایف خود داشته باشند.
**4. ارزیابی سالانه:**
بر اساس CQI-15، شرکتها ملزم به انجام ارزیابیهای سالانه از سیستمهای جوشکاری خود هستند. این ارزیابیها باید توسط افراد مجرب انجام شود و نتایج آن بهطور کامل مستند شود.
**5. بهبود مستمر:**
استاندارد CQI-15 تأکید زیادی بر بهبود مستمر فرآیندهای جوشکاری دارد. تحلیل دادههای جمعآوری شده، بازخورد مشتریان و نتایج ارزیابیها باید برای بهبود فرآیندها مورد استفاده قرار گیرند.
**6. هماهنگی با IATF 16949:**
CG,NI-15K بهعنوان مکملی برای استاندارد IATF 16949 در نظر گرفته میشود و بهطور خاص بر فرآیندهای جوشکاری مقاومتی تمرکز دارد.
**7. نتیجهگیری:**
استاندارد CQI-15 یک ابزار مهم برای تضمین کیفیت و بهبود فرآیندهای جوشکاری مقاومتی در صنعت خودروسازی است. اجرای موثر این استاندارد به کاهش نقصها، افزایش کارایی و بهبود کلی کیفیت محصولات کمک میکند.
دانلود IATF 16949 AIAG CQI 15
پارامترهای موثر بر میزان و تنظیم جریان الکتریکی در جوش نقطهای
پارامترهای موثر بر میزان و تنظیم جریان الکتریکی در جوش نقطهای بسیار حیاتی هستند، زیرا این پارامترها بر کیفیت و استحکام نقاط جوش تأثیر مستقیم دارند. در ادامه به بررسی این پارامترها پرداخته میشود:
### 1. **ضخامت قطعات فلزی:**
– **افزایش ضخامت:** با افزایش ضخامت قطعات فلزی، میزان جریان الکتریکی باید افزایش یابد تا اطمینان حاصل شود که حرارت کافی برای ایجاد نقطه جوش مناسب فراهم میشود.
– **کاهش ضخامت:** برای قطعات نازکتر، جریان الکتریکی باید کاهش یابد تا از سوختگی یا سوراخ شدن قطعات جلوگیری شود.
### 2. **نوع و جنس فلز:**
– **رسانایی الکتریکی فلز:** فلزاتی که رسانایی الکتریکی بالاتری دارند (مانند آلومینیوم) نیاز به جریان الکتریکی بالاتری دارند، زیرا گرمای کمتری در نقطه جوش تولید میشود.
– **سختی و استحکام فلز:** فلزات سختتر و قویتر ممکن است نیاز به جریان الکتریکی بیشتری داشته باشند تا به دمای مناسب برای ذوب شدن برسند.
### 3. **شکل و اندازه الکترودها:**
– **سطح تماس الکترودها:** الکترودهایی با سطح تماس بزرگتر، جریان الکتریکی را بر روی ناحیه بزرگتری توزیع میکنند که ممکن است نیاز به جریان بالاتری داشته باشد. الکترودهای کوچکتر جریان متمرکزتری ایجاد میکنند و ممکن است نیاز به تنظیمات دقیقتری داشته باشند.
– **وضعیت الکترودها:** سایش یا آلودگی الکترودها میتواند مقاومت الکتریکی را تغییر دهد، که این امر ممکن است نیاز به تنظیم جریان الکتریکی داشته باشد.
### 4. **فشار الکترودها:**
– **فشار بالا:** با افزایش فشار الکترودها، مقاومت الکتریکی در نقطه تماس کاهش مییابد که ممکن است نیاز به جریان بالاتری برای تولید حرارت کافی داشته باشد.
– **فشار پایین:** فشار پایینتر باعث افزایش مقاومت و ایجاد گرمای بیشتر میشود. بنابراین، جریان باید کاهش یابد تا از سوختگی جلوگیری شود.
### 5. **زمان اعمال جریان الکتریکی:**
– **زمان کوتاهتر:** در صورت کاهش زمان اعمال جریان، برای ایجاد حرارت کافی، جریان الکتریکی باید افزایش یابد.
– **زمان طولانیتر:** با افزایش زمان، جریان الکتریکی میتواند کمتر باشد، زیرا حرارت به مرور زمان تجمع مییابد.
### 6. **شرایط سطحی قطعات:**
– **تمیزی سطح:** سطوح آلوده یا دارای اکسید ممکن است مقاومت الکتریکی را افزایش داده و نیاز به جریان بالاتری داشته باشند.
– **وجود پوششها:** پوششهای محافظ یا آلیاژهای سطحی ممکن است نیاز به تنظیم جریان داشته باشند تا از یکپارچگی جوش اطمینان حاصل شود.
### 7. **دمای محیط:**
– **دمای بالاتر محیط:** دمای بالاتر ممکن است مقاومت فلز را کاهش داده و نیاز به جریان کمتری برای جوشکاری داشته باشد.
– **دمای پایینتر محیط:** دمای پایینتر ممکن است باعث افزایش مقاومت و نیاز به جریان بالاتری شود.
### 8. **فاصله بین الکترودها:**
– **فاصله زیاد:** با افزایش فاصله بین الکترودها، مقاومت مسیر الکتریکی افزایش یافته و ممکن است نیاز به جریان بالاتری داشته باشد.
– **فاصله کم:** فاصله کم ممکن است مقاومت را کاهش دهد و نیاز به جریان کمتری برای دستیابی به نقطه جوش مناسب وجود داشته باشد.
### 9. **فرکانس جریان:**
– **فرکانس بالاتر:** جریان الکتریکی با فرکانس بالا (مانند جریانهای متناوب با فرکانس بالا) میتواند به نفوذ بهتر گرما کمک کند و ممکن است نیاز به تنظیم جریان داشته باشد.
– **فرکانس پایینتر:** جریانهای با فرکانس پایینتر ممکن است نیاز به جریان الکتریکی بیشتری داشته باشند.
### 10. **دستگاه جوشکاری و شرایط فنی آن:**
– **دقت و کارایی دستگاه:** دستگاههای جوشکاری با تکنولوژی پیشرفته معمولاً دارای تنظیمات دقیقتری هستند که میتوانند نیاز به جریان الکتریکی را بهطور دقیق تنظیم کنند.
– **نگهداری دستگاه:** دستگاههای جوشکاری که بهدرستی نگهداری شدهاند، به تنظیمات جریان الکتریکی بهینه نیاز دارند. مشکلاتی مانند سایش کابلها یا اتصالات ضعیف میتوانند بر جریان تأثیر بگذارند.
زمان جوشکاری
در جوشکاری نقطهای قطعات خودرو، زمان جوشکاری یکی از پارامترهای کلیدی است که بر کیفیت و استحکام نقاط جوش تأثیر میگذارد. بر اساس استاندارد IATF 16949، که یک استاندارد مدیریت کیفیت ویژه صنعت خودروسازی است، باید پارامترهای مختلفی برای تعیین و کنترل زمان جوشکاری در نظر گرفته شوند. در ادامه، به پارامترهای موثر بر زمان جوشکاری در جوشکاری نقطهای قطعات خودرو میپردازیم:
### 1. **ضخامت قطعات فلزی:**
– **ضخامت بیشتر:** با افزایش ضخامت قطعات فلزی، زمان جوشکاری باید افزایش یابد تا حرارت کافی برای ذوب و جوش مناسب فراهم شود.
– **ضخامت کمتر:** برای قطعات نازکتر، زمان جوشکاری باید کاهش یابد تا از ذوب بیش از حد و سوراخ شدن قطعات جلوگیری شود.
### 2. **جنس و نوع فلز:**
– **رسانایی حرارتی فلز:** فلزاتی با رسانایی حرارتی بالا (مانند آلومینیوم) ممکن است نیاز به زمان جوشکاری بیشتری داشته باشند تا به دمای مورد نظر برسند.
– **استحکام فلز:** فلزات با استحکام بالاتر معمولاً نیاز به زمان جوشکاری طولانیتری دارند تا نقطه جوش با استحکام کافی ایجاد شود.
### 3. **فشار الکترودها:**
– **فشار بالا:** افزایش فشار الکترودها ممکن است نیاز به زمان جوشکاری کوتاهتری داشته باشد، زیرا فشار بیشتر باعث کاهش مقاومت الکتریکی و تولید حرارت بیشتر میشود.
– **فشار پایین:** فشار کمتر نیاز به زمان جوشکاری بیشتری دارد تا حرارت کافی برای ایجاد جوش تأمین شود.
### 4. **جریان الکتریکی:**
– **جریان بالا:** اگر جریان الکتریکی بالاتر باشد، زمان جوشکاری میتواند کوتاهتر باشد، زیرا گرمای بیشتری در زمان کمتری تولید میشود.
– **جریان پایین:** جریان الکتریکی کمتر ممکن است نیاز به زمان جوشکاری طولانیتری داشته باشد تا حرارت مورد نیاز برای جوش تولید شود.
### 5. **شکل و اندازه الکترودها:**
– **الکترودهای بزرگتر:** الکترودهایی با سطح تماس بزرگتر ممکن است نیاز به زمان جوشکاری بیشتری داشته باشند تا حرارت بهطور کامل در سطح وسیعتر پخش شود.
– **الکترودهای کوچکتر:** الکترودهایی با سطح تماس کوچکتر میتوانند با زمان جوشکاری کوتاهتری به نتایج مطلوب برسند، زیرا گرما در ناحیه کوچکتری متمرکز میشود.
### 6. **کیفیت سطح قطعات:**
– **تمیزی سطح:** سطوح تمیز و بدون آلودگی به کاهش مقاومت و نیاز به زمان جوشکاری کوتاهتر کمک میکنند.
– **آلودگی یا اکسیداسیون:** سطوح آلوده یا اکسیده ممکن است نیاز به زمان جوشکاری بیشتری داشته باشند تا حرارت کافی برای ذوب و جوش فراهم شود.
### 7. **دمای محیط:**
– **دمای بالاتر محیط:** ممکن است زمان جوشکاری کوتاهتر باشد، زیرا فلز به دمای جوش نزدیکتر است.
– **دمای پایینتر محیط:** زمان جوشکاری ممکن است افزایش یابد تا حرارت کافی برای ذوب فلز تولید شود.
### 8. **فرکانس جریان الکتریکی:**
– **فرکانس بالا:** جریانهای با فرکانس بالا (مانند جریانهای متناوب با فرکانس بالا) ممکن است زمان جوشکاری کوتاهتری نیاز داشته باشند، زیرا این جریانها به تولید گرمای سریعتر کمک میکنند.
– **فرکانس پایین:** زمان جوشکاری ممکن است طولانیتر باشد، زیرا تولید حرارت به زمان بیشتری نیاز دارد.
### 9. **نوع فرآیند جوشکاری و تنظیمات دستگاه:**
– **دقت تنظیمات دستگاه:** دستگاههای جوشکاری با دقت بالا به تنظیمات دقیق زمان جوشکاری نیاز دارند تا از کیفیت جوش اطمینان حاصل شود.
– **نوع فرآیند (AC یا DC):** بسته به نوع فرآیند جوشکاری (جریان متناوب یا مستقیم)، زمان جوشکاری ممکن است متفاوت باشد.
### 10. **تعداد و موقعیت نقاط جوش:**
– **نقاط جوش نزدیک به هم:** زمان جوشکاری باید به گونهای تنظیم شود که از تجمع بیش از حد حرارت جلوگیری کند، بهویژه زمانی که نقاط جوش نزدیک به هم هستند.
– **نقاط جوش دور از هم:** زمان جوشکاری میتواند طولانیتر باشد تا اطمینان حاصل شود که هر نقطه به درستی جوش داده شده است.
فشار الکترودها :
تنظیم فشار الکترودها در جوشکاری نقطهای به چندین عامل کلیدی وابسته است که بر کیفیت، استحکام، و کارایی نقاط جوش تأثیر میگذارند. این عوامل عبارتاند از:
### 1. **ضخامت قطعات فلزی:**
– **ضخامت بیشتر:** قطعات ضخیمتر نیاز به فشار بالاتری دارند تا الکترودها بهدرستی به سطح فلز نفوذ کنند و تماس کامل و مؤثر برقرار شود.
– **ضخامت کمتر:** برای قطعات نازکتر، فشار کمتری لازم است تا از لهشدن یا سوراخ شدن قطعات جلوگیری شود.
### 2. **نوع و جنس فلز:**
– **فلزات نرمتر (مثل آلومینیوم):** این فلزات به فشار کمتری نیاز دارند تا از تغییر شکل بیش از حد و کاهش کیفیت جوش جلوگیری شود.
– **فلزات سختتر (مثل فولاد):** این فلزات به فشار بیشتری نیاز دارند تا اطمینان حاصل شود که الکترودها بهخوبی تماس برقرار میکنند و جوش با کیفیت ایجاد میشود.
### 3. **شکل و اندازه الکترودها:**
– **الکترودهای بزرگتر:** این نوع الکترودها به فشار بیشتری نیاز دارند تا نیروی کافی برای ایجاد جوش در ناحیه وسیعتری تأمین شود.
– **الکترودهای کوچکتر:** فشار کمتری نیاز است، زیرا نیروی اعمالی در یک ناحیه کوچکتر متمرکز میشود.
### 4. **سطح تماس الکترودها:**
– **سطوح صاف و تمیز:** الکترودها در سطوح صاف و تمیز به فشار کمتری نیاز دارند، زیرا تماس بهطور مؤثر برقرار میشود.
– **سطوح ناهموار یا آلوده:** ممکن است نیاز به فشار بیشتری داشته باشد تا از اطمینان از تماس کامل و جلوگیری از نقص در جوش اطمینان حاصل شود.
### 5. **تنظیمات جریان الکتریکی:**
– **جریان الکتریکی بالا:** در این حالت، فشار الکترودها باید بیشتر باشد تا از سوختگی یا نفوذ بیش از حد جوش جلوگیری شود.
– **جریان الکتریکی پایین:** در این حالت، فشار کمتر کافی است، زیرا گرمای تولید شده کمتر است و نیاز به نیروی کمتری برای ایجاد جوش وجود دارد.
### 6. **زمان جوشکاری:**
– **زمان کوتاهتر:** برای زمانهای جوشکاری کوتاه، فشار بیشتری نیاز است تا تماس به سرعت و به طور مؤثر برقرار شود.
– **زمان طولانیتر:** فشار کمتری ممکن است کافی باشد، زیرا زمان بیشتری برای ایجاد جوش وجود دارد.
### 7. **دمای محیط:**
– **دمای پایینتر محیط:** ممکن است نیاز به افزایش فشار باشد تا حرارت بیشتری از طریق مقاومت ایجاد شود.
– **دمای بالاتر محیط:** ممکن است فشار کمتری نیاز باشد، زیرا فلزات در دماهای بالاتر انعطافپذیرتر هستند.
### 8. **طرح و طراحی قطعه:**
– **قطعات با طراحی پیچیده:** ممکن است نیاز به تنظیم دقیقتر فشار باشد تا از تغییر شکل ناخواسته یا تغییر در ابعاد قطعه جلوگیری شود.
– **قطعات ساده:** در این حالت، تنظیم فشار الکترودها سادهتر است و نیاز به تنظیمات پیچیده ندارد.
### 9. **کیفیت سطح و پوشش قطعات:**
– **قطعات بدون پوشش:** این قطعات به فشار کمتری نیاز دارند، زیرا تماس بهطور طبیعی و مؤثر برقرار میشود.
– **قطعات با پوشش:** قطعاتی که دارای پوشش هستند ممکن است نیاز به فشار بیشتری داشته باشند تا از طریق پوشش به سطح فلز نفوذ کند.
### 10. **نگهداری و وضعیت دستگاه:**
– **الکترودهای تمیز و تازه:** این الکترودها به فشار کمتری نیاز دارند، زیرا تماس بهتر و مؤثرتری برقرار میشود.
– **الکترودهای فرسوده:** فشار بیشتری ممکن است لازم باشد تا بهخوبی به فلز نفوذ کند و کیفیت جوش تضمین شود.
دانلود کتاب جوشکاری
به امید فردای روشن برای ایران جانمان
برای مشاوره IATF 16949 و الزامات پژو یا گرید A ساپکو یا الزامات جدید ساپکو و ایران خودرو ISSR 2 و SSQR2 با ما در تماس باشید .
حسین زینل/مجتبی موسوی
09125076715
دیدگاهتان را بنویسید